Share
Pin
Tweet
Send
Share
Send

Das Wichtigste an der Bormaschine ist natürlich der Elektromotor. Der Motor für eine Maschine mit durchschnittlichem Preis- und Qualitätsniveau sollte ungefähr 16 bis 18.000 Umdrehungen pro Minute produzieren. Dies ist völlig ausreichend, um hölzerne Knüppel und Kunsthandwerk, Knochen, Kunststoff, Aluminium und Duraluminium sowie nicht feste Mineralien und Steine zu verarbeiten. Motoren ab 20.000 Umdrehungen pro Minute sind bereits in der Lage, mit festen Mineralien und Metallen zu arbeiten ... So kam es, dass ich auf einer Fernbedienung einen funktionierenden Motor von einem Spielzeugmotorboot bekam, der mir als Ersatzteil übergeben wurde. Die Reparatur dieses Spielzeugs schien nicht kosteneffektiv zu sein. Elektronik, die durch Wasser durchgebrannt war, war etwas billiger als das Spielzeug. Ihr Motor selbst wurde jedoch nicht verletzt. Der Motor dort stand bei 9 Volt, ziemlich groß, leistungsstark und ziemlich einfallsreich - es ist verständlich, dass er in ein Spielzeug gesteckt wird, um ihn schnell durch das Wasser zu schieben, und zu diesem Zweck muss der Motor leistungsstark und einfallsreich sein.

Leider habe ich kein Gerät zum Messen von Umdrehungen, aber es fühlte sich an, als wollte ich die Welle eines funktionierenden Motors mit meinen Fingern stoppen. Es wurde klar, dass damit eine einfache Bor-Maschine hergestellt werden kann, die zumindest für die Arbeit mit Holz, Kunststoff und Knochen geeignet ist Wird definitiv passen.
Wird brauchen
- Der Motor von einem Spielzeugboot (oder ähnlich, die gleichen Eigenschaften - 9-12 Volt).
- Eine geeignete Spannungsversorgung oder ein passender Adapter zur Stromversorgung des Motors.
- Stecker und Stecker dran.
- Startknopf.
- Rohr mit einem Innendurchmesser unter dem Motor und einer Länge siehe 15-17.
- Plastikfolie, 2-3 mm dick. (für die Enden).
- Zweiter Kleber und Soda.
- Miniatur-Spannzangenfutter mit 3,17 mm Anschluss. und klemmen von 0,3 bis 3,5 mm.
- Alle kupferisolierten Drähte.
Werkzeug für die Arbeit erforderlich:
- Lötkolben mit Zinn und Flussmittel.
- Datei.
- Schleifpapier, mittlere Körnung.
- Ein Messer mit einer starken und scharfen Klinge (vorzugsweise ein technisches Skalpell).
- Schmirgelmaschine oder Brenner (zum Schneiden von Kunststoff).
Herstellung von Bohrmaschinen
Zuerst müssen Sie den Motor selbst überprüfen - er sollte gleichmäßig und geruchsneutral arbeiten und sich beim Anschließen nicht sofort aufheizen. Sie können eine Patrone anprobieren.

In Zukunft ist eine leichte Erwärmung während des Betriebs normal. Mit Hilfe des Akkus und der LED können Sie außerdem die Starttaste und den Stecker mit seinem Anschluss auf Funktionalität prüfen. Es ist besser, die Störung zu Beginn der Montage zu erkennen und zu beseitigen als am Ende. Da die von uns geplante Maschine einfach ist und keine Geschwindigkeitsschalter besitzt, kann der Startknopf auf einfachste Weise mit einem einzigen Tastendruck betätigt werden, z. B. durch Drücken eines Schlüssels auf einer Fernbedienung. Also; gedrückt - es funktioniert, freigegeben - es funktioniert nicht mehr. Es ist auch sicher; In einer unvorhergesehenen, unerwünschten Situation ziehen wir unwillkürlich den Finger vom Knopf und vermeiden so mögliche Verletzungen oder Beschädigungen der umliegenden Gegenstände. Der Stecker mit dem Stecker kann nach Ihrem Ermessen gewählt werden. Hauptsache, sie passen zusammen und sind Arbeiter.

Wir nehmen also ein Rohr mit passendem (oder annähernd passendem!) Durchmesser. Ich habe ein Stück Pfeife von einem alten, unnötigen Staubsauger abgeschnitten. Wir probieren einen Motor an. Wenn das Rohr etwas zu groß ist - es ist nicht unheimlich (Hauptsache nicht zu klein!), Wickeln Sie einfach mehrere Windungen Isolierband auf den Motor, damit es zu einer geeigneten Stärke wird. Zusätzlich wirkt ein weiches und flexibles elektrisches Klebeband als eine Art Stoßdämpfer - es wird Schwingungen dämpfen und absorbieren, die sich unvermeidlich bilden, wenn der Motor läuft. Wenn das Rohr und der Motor zusammenkommen, lassen Sie uns die Enden behandeln. Messen Sie dazu die Breite der Stelle des Motors, mit der wir ihn am Ende befestigen, bohren Sie ein geeignetes Loch in die Kunststoffplatte und setzen Sie den Motor ein. Es stellt sich so heraus:

Anschließend den Motor in das Rohr einführen, bis die Kunststoffplatte am Ende anliegt. Wir zeichnen einen Marker um die Kontur.

Wir entfernen das Blech vom Motor und schneiden mit Hilfe eines Brenners oder einer Schmirgelmaschine eine runde Stirnwand entlang der Konturen. Wir machen auch das Heck.


Nur hier ist die Situation einfacher - hier ist es nicht erforderlich, den Mittelpunkt zu berechnen, in dem ein Loch für den Steckverbinder gemacht werden soll. Wir messen die Breite des Verbinders und bohren ungefähr in der Mitte der fertigen Endplatte ein geeignetes Loch. Lassen Sie uns jetzt mit dem Knopf beschäftigen. Wir werden den für uns günstigsten Ort auswählen, an dem er sich befinden wird. Wir messen die Parameter der Schaltfläche und übertragen sie an den ausgewählten Ort.

Wir schneiden (oder bohren) ein passendes Loch.


Nehmen Sie als nächstes einen doppelten Kupferdraht (siehe 20).

Wir bestimmen seine Mitte, in dieser Mitte schneiden wir einen der Kerne in zwei Hälften, löten den abgeschnittenen Kern in der Mitte auf die Kontakte des Knopfes. Es stellte sich heraus, dass es sich um ein zweiadriges Kabel handelte, in dessen Mitte sich ein Unterbrecher an einem der Adern befand. Hier ist einer:
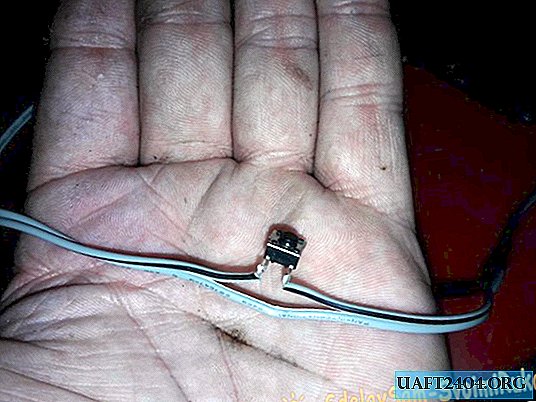
Jetzt führen wir den Draht mit dem Knopf in das Rohr, finden mit dem Knopf das Loch dafür und stecken den Knopf von innen in dieses Loch. Wir reparieren es mit Sekundenkleber.

Nur vorsichtig, damit der Kleber nicht in die Knopfmechanik gelangt. Dann verlöten wir die vorderen Enden des Kabels mit den Motorkontakten. Wir befestigen die Endplatte mit Klebstoff am Motor.

Die Rohrenden mit Klebstoff bestreichen und den Motor mit der Platte in das Rohr einführen, bis die Endplatte an den mit Klebstoff beschichteten Rohrenden anliegt. Drücken Sie fest für 10-15 Sekunden, bis der Klebstoff aushärtet.

Auf die gleiche Weise bringen wir das hintere Ende an und vergessen nicht, den Steckverbinder mit den Enden des daran angelöteten Kabels daran zu kleben.



Die Hauptarbeit ist abgeschlossen.

Jetzt gleichen wir mit einer Feile und einem Schmirgeltuch die Ecken der Enden aus, sodass sie bündig mit den Wänden des Gehäuses abschließen.

Als nächstes stecken Sie den Stecker von unserem Stecker in das Kabel des Netzteils.



Vergessen Sie nicht die Polarität. Wenn Sie es verwechseln, ist es okay, im Prinzip passiert es nicht, es ist nur so, dass sich der Schaft in die falsche Richtung dreht und wir natürlich nichts bohren können. Wenn Sie dieses Gerät jedoch nur zum Schneiden kleiner Gegenstände oder zum Schärfen von Messern verwenden möchten, spielt die Polarität keine besondere Rolle. Es bleibt nur die Spannzange auf der Welle zu installieren, und Sie können es verwenden. Ein Spannzangenfutter, Diamantfedern für eine Bohrmaschine und dünne Bohrer, die ich in einem Online-Shop bestellt habe.

Leider ist bisher nur eine Patrone gekommen, so dass ich auf dem Video nur die Schneid- und Schärfeigenschaften des zusammengebauten Gerätes demonstrieren konnte. Und dann mit hausgemachten Düsenfeilen. Schärfen Sie Metall, schleifen Sie und schneiden Sie Plastik, es ist ziemlich schwungvoll, was bedeutet, dass das Bohren gut sein wird.
Share
Pin
Tweet
Send
Share
Send